In a globally connected world where partnerships stretch across continents and industries, Malaysian customers visit our company to witness firsthand the strengths, capabilities, and commitment to excellence we uphold. Recently, a delegation of esteemed Malaysian customers visited Elite Piping Manufacture Co., Ltd.’s factory to observe the manufacturing processes, quality control procedures, and operational excellence that define our operations. This visit by Malaysian customers not only reinforced the existing business relationships but also opened doors for future collaborations and opportunities, solidifying the foundation of our long-term partnerships.
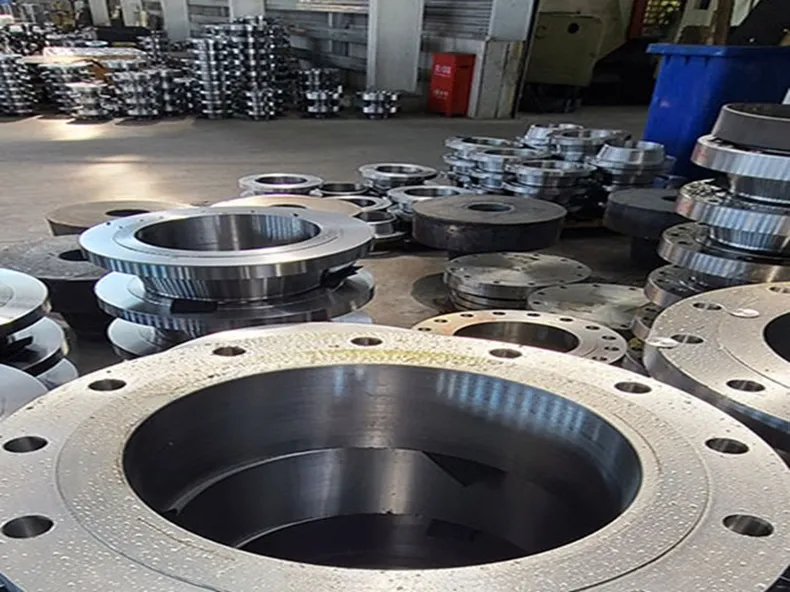
Pre-Visit Preparations Of Malaysian Customers Visit Our Company To Observe The Factory
A detailed itinerary was prepared when Malaysian customers visit our company, covering the full day’s schedule. This included a factory tour, technical presentations, Q&A sessions, and time allocated for discussions on both current projects and future collaborations. The visit of Malaysian customers was carefully organized to ensure a productive and insightful experience for all involved.
When Malaysian customers visit our company, we prioritized their safety by preparing a thorough safety briefing, aligned with our factory’s high safety standards. Personal protective equipment (PPE) was provided for all visitors, and each section of the factory was carefully assessed to ensure that operations would be easily understandable to external parties. This attention to detail ensured that the Malaysian customers’ visit to our company was both safe and informative.
In preparation for the Malaysian customer’s visit to our company, our engineering team developed comprehensive presentations and technical documentation. These materials highlighted our manufacturing capabilities, the raw materials we use, the advanced technology we implement, and the strict quality control measures we follow. This ensured that when Malaysian customers visit our company, their technical queries would be thoroughly addressed.
Recognizing the importance of cultural sensitivity, we made special arrangements to cater to the specific preferences of our Malaysian customers when they visit our company. This included accommodating their dietary requirements and providing a warm, culturally appropriate reception to ensure a welcoming experience for Malaysian customers during their visit.
On the day of the visit, our Malaysian customers arrived in the morning and were warmly welcomed by senior management and our designated hospitality team. A formal welcome ceremony took place in the conference room, where our General Manager personally addressed the Malaysian customers. This initial interaction was vital in establishing a friendly atmosphere for the day and highlighted the significance we placed on the Malaysian customers’ visit.
During the welcome ceremony, we provided an overview of our company’s history, corporate values, and the various industries we serve. This preliminary introduction set the stage for the more technical aspects of the visit and sparked great interest among the Malaysian customers visit our company in learning about our company’s journey, paving the way for deeper engagement.
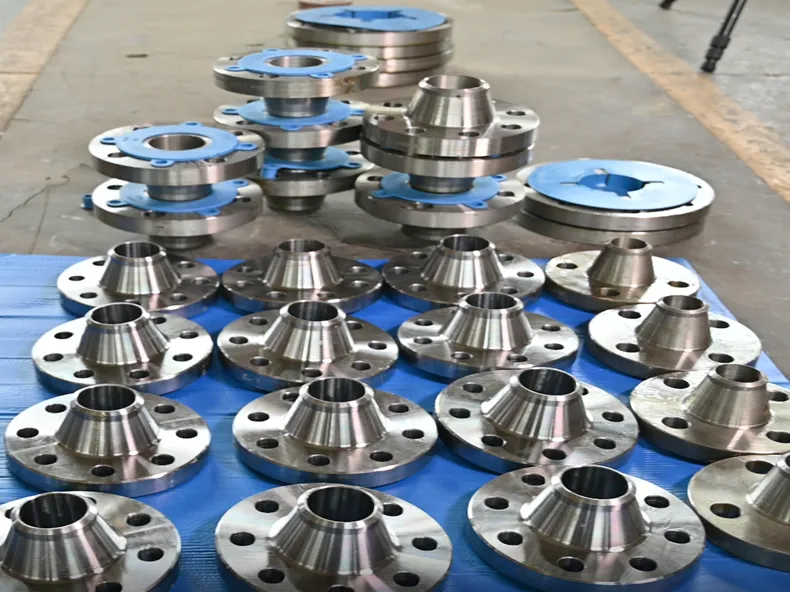
Factory Tour: A Firsthand Look At Our Operations
We guided our Malaysian customers through the cutting and forging areas of flanges and pipe fittings, where they witnessed the precision involved in cutting and forging raw materials into components.
The level of automation in these processes particularly impressed Malaysian customers, as it significantly minimizes human error and enhances product quality. This firsthand observation during the Malaysian customers visit our company highlighted our commitment to excellence in manufacturing.
As our Malaysian customers visit our company, we took them to the heat treatment and machining sections, where they learned how various products undergo different types of heat treatments to enhance their mechanical properties.
This segment of the tour showcased our investment in cutting-edge CNC machines, which enable high precision in complex machining tasks. The Malaysian customers were especially interested in our strict adherence to heat treatment cycles and machining tolerances, underscoring our commitment to quality.
A significant highlight of the visit was our quality control laboratory, where Malaysian customers observed the rigorous testing methods we use to ensure product compliance with global standards. During their visit to our company, they witnessed various testing processes, including material testing and non-destructive testing (NDT) methods such as ultrasonic testing and X-ray inspection.
This experience demonstrated to the Malaysian customers visit our company that we leave no room for error in maintaining product integrity. They were particularly impressed by the comprehensive range of testing equipment and the certification protocols that govern our operations.
Strengthening Relationships Over Lunch
After the formal presentations and Q&A session, the Malaysian delegation was invited to a lunch organized in their honor. This provided an opportunity for more informal interactions, where both parties could discuss business matters in a relaxed atmosphere. The lunch also allowed us to learn more about the Malaysian market and explore potential future collaborations in greater detail.
Post-Visit Feedback And Future Collaboration Opportunities
The day concluded with a final discussion, during which our Malaysian customers provided valuable feedback on the visit. They expressed their satisfaction with the transparency, professionalism, and quality standards they had observed. Importantly, they indicated a strong interest in expanding their business with us, with the possibility of placing larger orders and developing custom products for the Malaysian market.
We left the meeting with a clear understanding of our customers’ needs and how we could better serve them in the future. Follow-up actions were discussed, including sending additional technical documentation, providing product samples, and arranging virtual meetings for further discussions.
GET IN TOUCH
Company:
Elite Piping Manufacture Co., Ltd.
Factory Address:
Office # 805, Building No. 6 Poly Metropolitan, Yongshum Town, Tongzhou District, Beijing, China.
Contact Person:
Michael
Contact Numbers:
+86 186 1829 1381
Email:
elite@elitepiping.com