Flanges are a type of connecting component frequently utilized in piping systems to join two pipes, fittings, or equipment. As we know, there are many materials used in the production of flanges, such as carbon steel, stainless steel, and alloy steel, which results in different types of flanges, including carbon steel flanges and stainless steel flanges.
Compared to stainless steel flanges, carbon steel flanges have somewhat lower corrosion resistance. However, they still offer excellent sealing performance and flexibility. During operation, they do not interfere with each other, allowing for easy disassembly of specific sections of the pipeline when needed. This special feature helps minimize damage caused by unexpected incidents during use, making carbon steel flanges particularly suitable for pipeline repair work. So, are you aware of the process for producing carbon steel flanges? What are the key considerations to keep in mind during the production of carbon steel flanges?
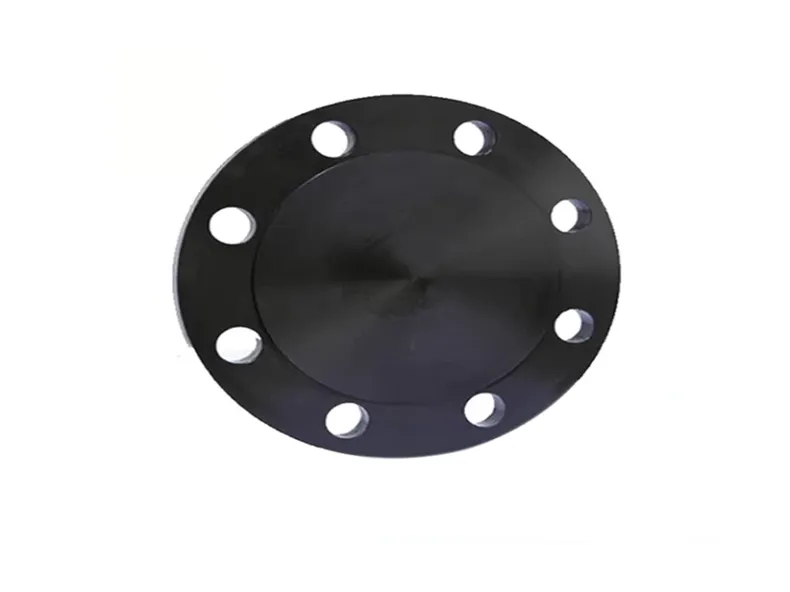
Choosing The Right Grade Of Carbon Steel
Typically contains up to 0.3% carbon. It is known for its excellent weldability and machinability but may have lower strength and hardness compared to higher carbon steels. This grade is suitable for applications with lower pressure and temperature requirements.
Contains approximately 0.3% to 0.6% carbon. It strikes a balance between strength and ductility, making it suitable for moderately demanding applications. Medium carbon steel is often used for flanges requiring higher strength and toughness.
Contains 0.6% to 1.0% carbon. This grade provides high strength and hardness but can be more challenging to weld and machine. It is suitable for applications where high strength is critical, but its brittleness and reduced ductility need to be managed.
Machining
Turning And Facing
Choosing the appropriate cutting tools and machining parameters is crucial for achieving the desired surface finish and dimensional accuracy.
Machining must be performed within specified tolerances to ensure the flanges fit correctly with other components and meet industry standards.
Achieving the required surface finish is important for sealing and aesthetic purposes.
Drilling And Threading
Accurate alignment of bolt holes is necessary to ensure proper mating with companion flanges and to prevent issues such as leakage or misalignment.
The quality of threading must be checked to ensure that it meets specified standards and provides a secure connection.
Ensuring precise dimensions and thread specifications is critical for reliable connections.
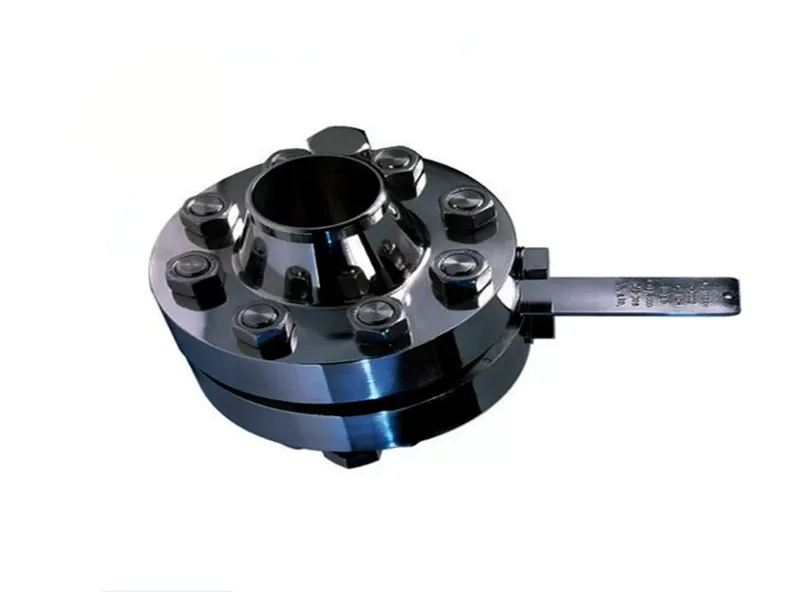
Forging Process
Heating
- Temperature Control
- Heating Equipment
Maintaining precise heating temperatures is crucial to prevent overheating, which can lead to grain growth and reduced mechanical properties, or underheating, which can result in incomplete forging and material defects.
The choice of heating equipment, such as electric or gas furnaces, can impact temperature control and consistency.
Forming
- Casting Design
- Forging Pressure
- Material Flow
The forging casting must be designed to ensure uniform material flow and avoid issues such as die wear, material flash, or defects. Proper die design is critical for achieving the desired shape and dimensions.
The pressure applied during forging affects the final properties of the flange. Insufficient pressure can result in weak or defective flanges, while excessive pressure can cause deformation or cracking.
Ensuring uniform material flow during forging helps avoid issues such as uneven thickness or internal defects.
Cooling
- Rate
- Methods
The cooling rate should be managed to avoid rapid cooling, which can lead to thermal stresses and brittleness. Controlled cooling or annealing may be required to achieve the desired properties.
Methods such as air cooling or controlled cooling environments can be used depending on the desired properties and application requirements.
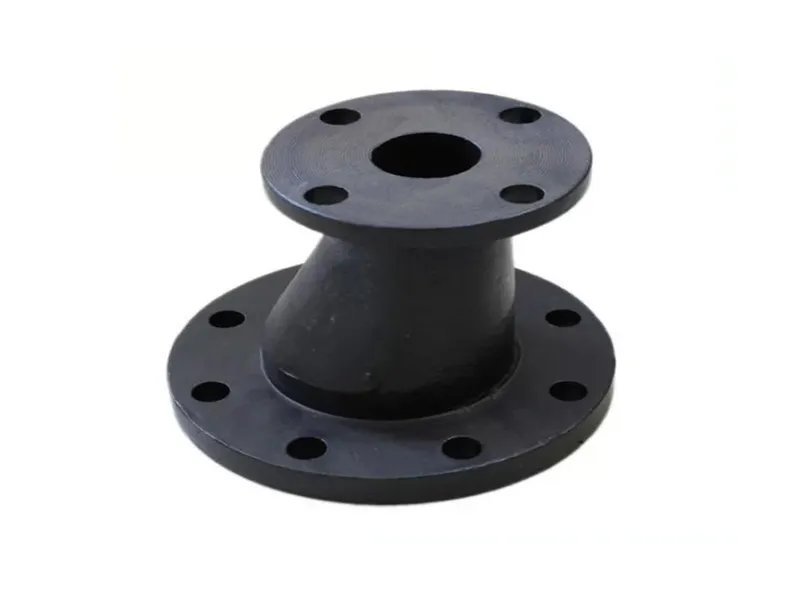
Considerations For Producing Carbon Steel Flanges
The carbon steel flange is assembled from two clamping base plates, two flange support plates, two vertical plates, and four reinforcement plates, all welded together.
To ensure the rigidity of the assembly, the weld seams between the connected plates should be bevel-welded and fully penetrated, with weld angles of 20-30 mm.
The flange support plates are drilled with corresponding bolt holes. A gap is left between the back of the small end flange and the support plate to accommodate a small manual jack.
Additionally, notches are made along the vertical plate direction on the flange support plate to facilitate the insertion of elbows into the fixture. When the fixture is clamped on the workbench, it must ensure that the flange surface being machined is concentric and parallel to the vertical lathe workbench.
To reduce the number of fixtures, this fixture should be adaptable to change clamping positions, ensuring that flanges on both ends of the elbow can be machined on a single fixture. Moreover, the fixture needs to have sufficient rigidity; otherwise, it will severely impact the machining quality of the flange seal groove.
GET IN TOUCH
Company:
Elite Piping Manufacture Co., Ltd.
Factory Address:
Office # 805, Building No. 6 Poly Metropolitan, Yongshum Town, Tongzhou District, Beijing, China.
Contact Person:
Michael
Contact Numbers:
+86 186 1829 1381
Email:
elite@elitepiping.com